Review
Big bag unloading stations ensure continuous and safe unloading of product and prevent the spread of dust into the environment.
Various types of bulk materials can be processed, ranging from free-flowing granules to difficult-to-flow sticky fine powders.
To take full advantage of big bags, well-designed systems are required. Bulk material type, big bag size, discharge medium, equipment, discharge speed, environmental aspects, ergonomics and safety are all important factors influencing the final design of the device.
Modular design
Allows you to easily configure them for each application. While standard models have a simple frame and discharge bins, high-end models have a complete solution on one main frame. Big bag unloading, product storage, dust collection, dosing and transport can be completed in one unit.
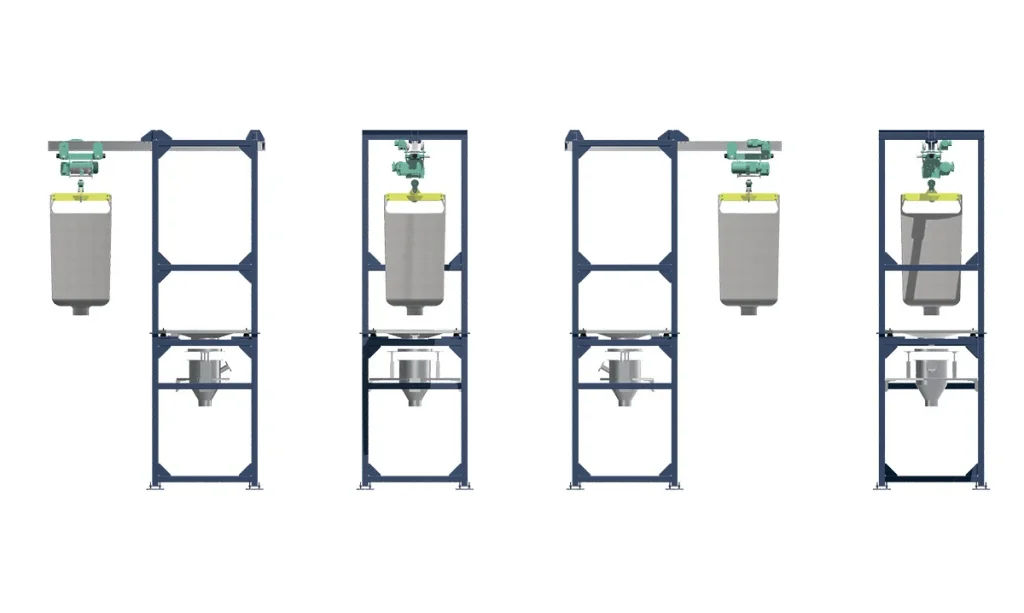
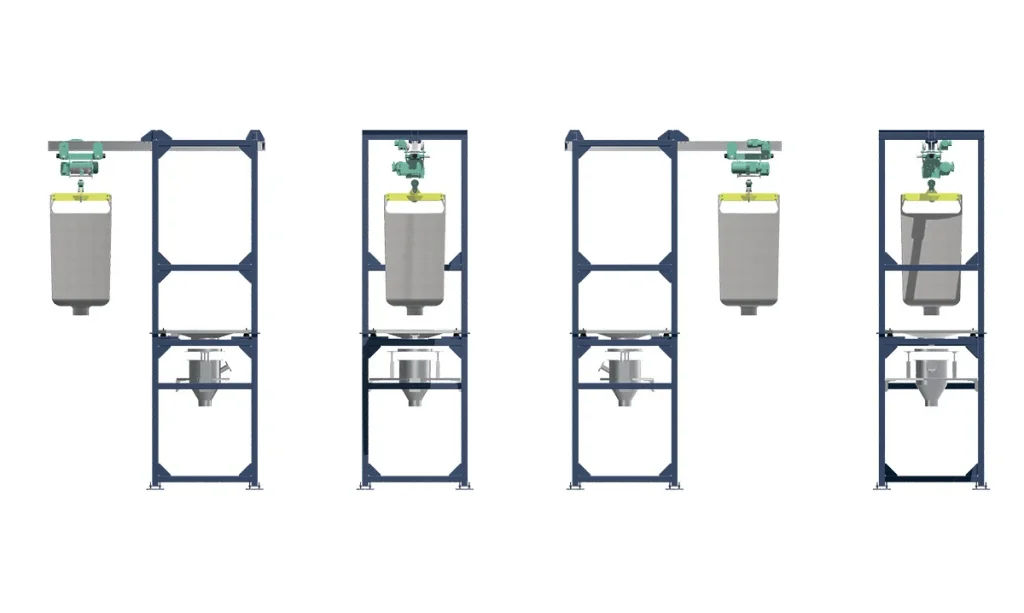
Unpacking stations in combination with other systems.
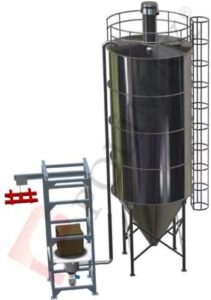
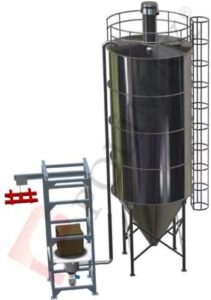
Loading silos using a pneumatic conveying system
Pneumatic conveying systems installed after the bulk material bag unloading units transfer bulk material through transport pipelines to fill silos. This configuration is convenient in cases where high travel speeds and long transport distances are required. In production lines where raw materials are stored in warehouses located far from the silos, big bag unloading stations can be installed adjacent to the warehouses and pneumatic conveying systems are used to fill the silos. This design eliminates the excessive use of forklifts and cranes to move bulk materials on the job site and improves overall efficiency.
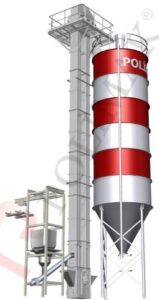
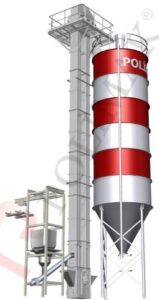
Mechanical conveyor systems for loading silos
Mechanical conveyors can be used to load silos from big bag unloading stations. Screw feeders, bucket elevators, rotary valves or chain conveyors are connected to big bag unloading stations to fill silos. The choice of conveying equipment directly depends on the transportation distance, height, material being moved and productivity. Bucket elevators are preferred for tall silos. Screw feeders are preferred for shorter silos and shorter distances. A big bag unloading system can be installed on top of the silo for faster filling. In this case, it is better to use rotary valves or butterfly valves, which provide simple flow control. Depending on the dust content of the bulk material, dust extraction systems may be required. As the silo is loaded, the air contained within it is released into the atmosphere and carries with it some dust. By aspirating the process, the collected dust is sent back to the silo and product loss is prevented.
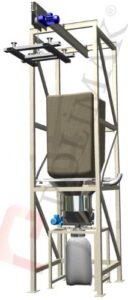
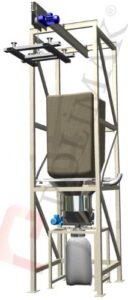
Big bag unloading and filling systems
Bulk material stored in large bags can be automatically filled into smaller bags. Big bag unloading systems have optional built-in bag filling units. For small filling volumes, these devices are installed under the big bag discharge hopper and provide a practical and cost-effective solution. Big bag unloading and bag filling operations can be performed on one compact system.
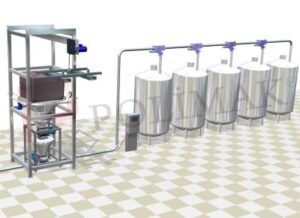
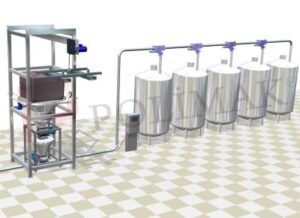
Unloading big bags and filling mixers
Raw materials supplied in bags can be transferred to mixing units using a combination of conveying equipment and unloading systems. Depending on the type of application, pneumatic or mechanical feeding systems may be used to fill the mixers. Big bag unloading stations can be manufactured with a built-in dosing system. The amount of raw materials loaded into the mixer is controlled automatically using a weighing and dosing system. Aspiration systems can be used to prevent dust from being released when filling the mixer.
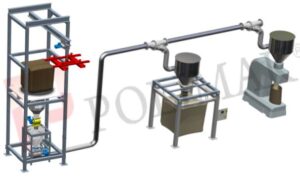
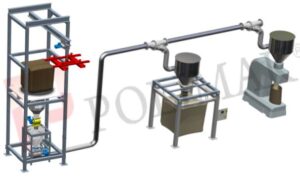
Unloading big bags and feeding into packaging systems
Dry bulk packaging systems are used to fill powdered or granular materials into bags, drums, etc. Bulk materials supplied in big bags must be transferred to packaging machines without interruption. The filling hopper of the packaging system must remain full during filling and packaging. Big bag unloading systems can monitor the product level in the feed hopper and automatically maintain a constant material level. Depending on the packing speed, mechanical conveying systems or pneumatic loading systems can be selected. Aspiration systems can be used to prevent dust from being released when filling the mixer.
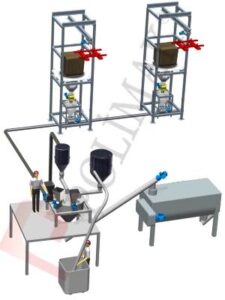
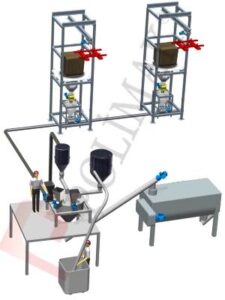
Unloading, dosing, weighing systems
Big bag unloading systems can deliver dry bulk solids in the form of powder and granules to weighing and dosing systems. The weighing system's hopper must remain full during dosing. Big bag unloading systems can monitor product levels in the feed hopper and automatically maintain a constant load. Depending on the dosing speed and transport distance, mechanical or pneumatic loading systems can be used. Aspiration systems can be used to prevent dust from being released when filling the mixer.
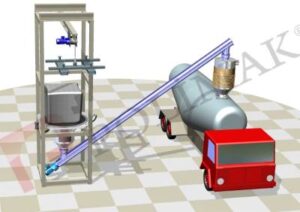
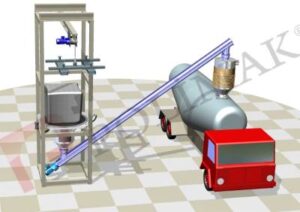
Systems for unloading big bags and loading bulk cargo into trucks
The big bag unloading station transfers bulk material from the big bags to the transport system. The transport system transfers it to the loading area of the truck. And the telescopic loading arm is used to fill the tanker without emitting dust. Since tank truck loading operations are carried out within a limited time, high-capacity big bag unloading systems and bulk material handling systems are used. To move material from the big bag unloading station to the tank truck loading chute over short distances, it is preferable to use screw conveyors. For transportation over long distances, it is better to use pneumatic transportation systems. To compensate for the flow of material, a storage hopper or silo may be located between the inlet and outlet above the loading chute of the forklift. Bulk bag unloading and truck filling systems are equipped with an automatic control system that monitors the product level in the truck and controls all equipment accordingly. An optional weighing system can be added to measure the amount of material loaded into the truck.
Our projects